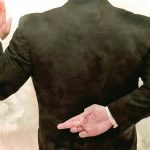
Sunday, July 22, 2018 by Edsel Cook
http://www.futuresciencenews.com/2018-07-22-research-team-finds-a-way-to-cheaply-create-nanotubes-made-from-carbon-dioxide.html
Potentially toxic carbon dioxide can now be transformed into invaluable carbon nanotubes. In a Science Direct article, researchers from Tennessee have reported creating a prototype device that can absorb CO2 from the air and turn it into “black gold.”
Carbon nanotubes possess a strength that exceeds steel and a conductivity superior to commonly used copper. These properties make them very useful in numerous fields such as electronics, environment clean-up, and healthcare. However, carbon nanotubes are very difficult to manufacture at the right size, making them uncommon and expensive to boot.
The Vanderbilt University (Vanderbilt) research team found a different means of producing the supermaterials. Using carbon dioxide drawn from the air as raw materials, they showed how they can produce the carbon nanotubes at a much lower cost than current methods.
Their technique not only negates the harmful effects of carbon dioxide emissions, it also shows how air pollution can be put to good use that will pay for the process of air purification. (Related: Carbon nanotube material removes 99% of heavy metals from water.)
Cary Pint, an assistant professor at Vanderbilt’s mechanical engineer department, explained that her research team used electrochemical means to break down carbon dioxide into carbon and oxygen molecules. The carbon was then collected and assembled into carbon nanotubes with nanometer accuracy.
“That opens the door to being able to generate really valuable products with carbon nanotubes,” said Pint, who served as the co-author of the research paper. “These could revolutionize the world.”
She published the findings of her team in the science journal ACS Applied Materials and Interfaces. Their paper explained how they took carbon dioxide coatings that had collected on stainless steel surfaces and turned them into nanoparticles, which were then synthesized into carbon nanotubes.
Their method required much less energy than current means of producing carbon nanotubes, such as the carbon arc discharge method and the laser method.
Vanderbilt student and study co-author Anna Douglas reported that the price of commercially available carbon nanotubes started at more than $100 per kilogram. In comparison, their recently developed method can produce higher quality supermaterials at a much cheaper cost, especially since it uses carbon dioxide taken from the air instead of the usual sources.
Their achievement is impressive given the difficulty of creating small nanotubes. The Ostwald ripening process causes carbon nanoparticles to increase their size. Larger nanoparticles mean larger nanotubes, which are nowhere as useful as their smaller versions and therefore a waste.
The Vanderbilt team was able to minimize the effect of Ostwald ripening by setting electrochemical parameters to reduce the possibility that a large nanoparticle will form. The parameters encouraged the formation of smaller nanoparticles that could be used to make nanotubes of the right size.
Pint and Douglas co-founded the start-up company SkyNano LLC to improve their carbon nanotube production process so that it can be scaled up for commercial use. Potential products that use carbon nanotubes include efficient anodes, cathodes, and electrodes for capacitators and batteries, absorbent materials that can remove oil and purify water for drinking, and lightweight flexible materials for building artificial muscles and tiny sensors.
“What we’ve learned is the science that opens the door to now build some of the most valuable materials in our world, such as diamonds and single-walled carbon nanotubes, from carbon dioxide that we capture from air through our process,” Pint said of their carbon nanotube production process.
Find more articles about new research regarding carbon at Discoveries.news.
Sources include: